Exploring the Cutting-Edge Advantages of Thermoset Molds in Modern Manufacturing
Time:
2025-06-24
1. Introduction
With the surge in demand for high-performance materials in manufacturing, thermoset molds have garnered significant attention. These molds, made from thermosetting plastics, undergo a chemical change when cured, solidifying into a rigid structure. This unique characteristic makes them ideal for various applications, offering manufacturers a range of advantages that traditional materials cannot match.
2. What Are Thermoset Molds?
Thermoset molds are created using polymeric materials that harden into an irreversible structure when cured, typically through the application of heat and pressure. Unlike thermoplastics, which can be remelted and reshaped, thermoset materials maintain their shape and strength under high temperatures and stress. This stability makes them suitable for applications where durability and resistance to deformation are critical.
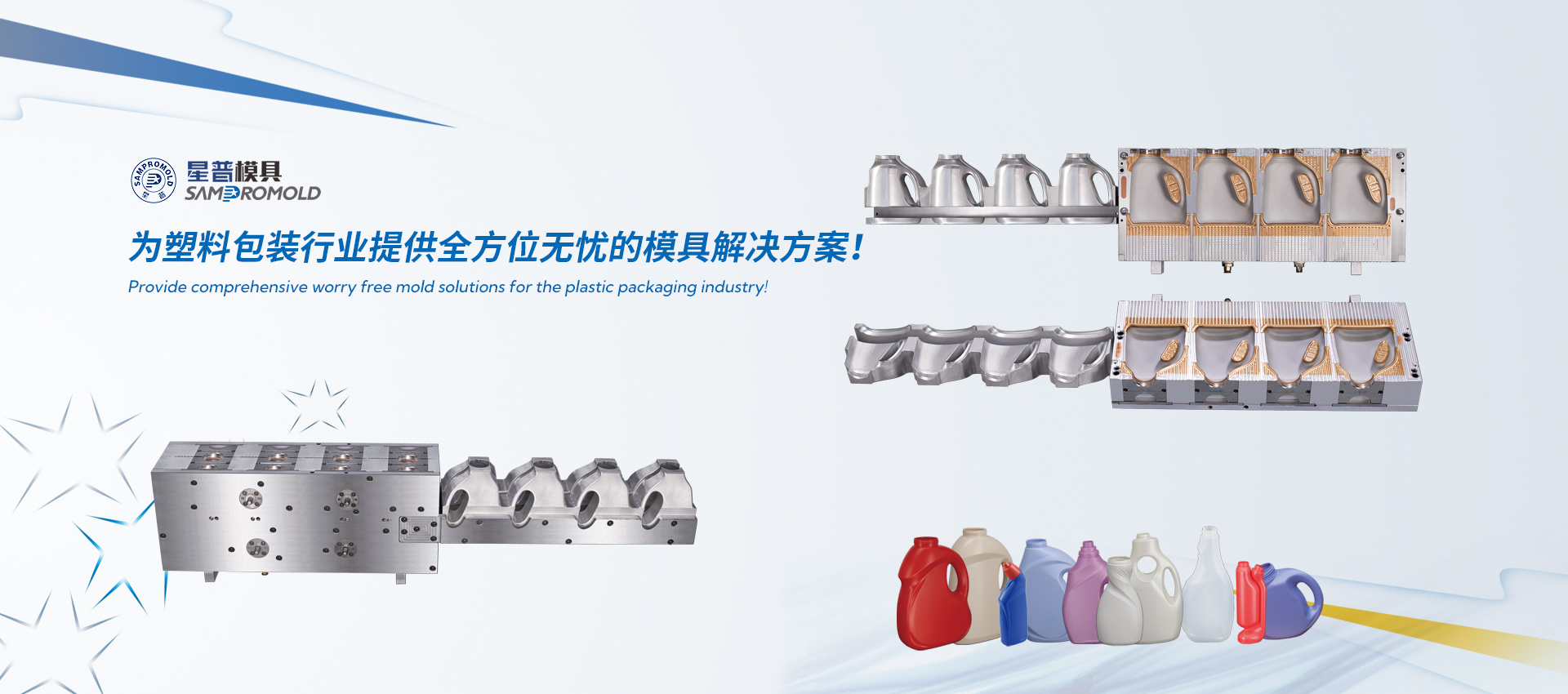
Common Types of Thermoset Materials
The most common thermoset materials used in manufacturing include:
- Epoxy Resins: Known for their excellent adhesion and mechanical properties, epoxy resins are widely used in various industries.
- Phenolic Resins: Renowned for their heat resistance and durability, phenolic resins are often utilized in electrical applications.
- Polyester Resins: These resins provide good mechanical properties and are often used in composite applications.
- Polyurethane: Known for their versatility, polyurethanes can be tailored for specific applications, offering a range of hardness and flexibility.
3. Benefits of Thermoset Molds in Manufacturing
The adoption of thermoset molds in manufacturing comes with numerous advantages that can significantly enhance production processes.
3.1 Durability and Strength
One of the primary benefits of thermoset molds is their inherent **durability**. These molds exhibit remarkable resistance to wear and tear, making them suitable for high-volume production runs. The strength of thermoset materials ensures that the finished products maintain their integrity under stress, leading to fewer defects and increased operational efficiency.
3.2 Heat Resistance
Thermoset molds are highly resistant to heat, making them ideal for applications where high temperatures are a concern. This property allows manufacturers to use them in **high-temperature environments** without worrying about deformation or failure, thus broadening their application scope.
3.3 Cost-Effectiveness
While the initial investment in thermoset molds may be higher than that of thermoplastics, their long lifespan and durability often result in lower overall costs. Manufacturers benefit from reduced replacement rates and lower maintenance costs, contributing to improved profitability in the long run.
3.4 Versatility in Design
Thermoset molds offer exceptional **design versatility**, enabling manufacturers to create complex shapes and detailed features. This capability allows for innovative designs that can meet specific customer requirements and market demands, enhancing product appeal and market competitiveness.
4. Applications of Thermoset Molds
The applications of thermoset molds span across various industries, including:
- Aerospace: Lightweight, durable components made from thermoset materials are essential in aerospace applications, contributing to fuel efficiency and performance.
- Automotive: Thermoset molds are employed in the production of parts such as dashboards, bumpers, and other structural components that require high durability.
- Electronics: The heat resistance of thermoset materials makes them suitable for electrical housings and insulators, where thermal stability is crucial.
- Consumer Goods: Thermoset molds are increasingly used in the manufacturing of household items, offering durability and aesthetic appeal.
5. Comparing Thermoset and Thermoplastic Molds
A key comparison arises between thermoset and thermoplastic molds, as both have their unique advantages and limitations. Understanding these differences can help manufacturers make informed decisions when selecting mold materials.
Thermoset Molds
- Excellent heat resistance
- Durable and long-lasting
- Irreversible once cured
- Best suited for high-strength applications
Thermoplastic Molds
- Can be remelted and reshaped
- Generally lighter than thermosets
- Faster production cycles
- More suitable for lower strength applications
The choice between the two ultimately depends on the specific application requirements, production volume, and desired properties of the final product.
6. The Future of Thermoset Mold Technology
The future of thermoset mold technology is promising, with continuous advancements driving innovations. Research is focusing on enhancing the properties of thermoset materials, making them even more versatile and efficient. Key areas of development include:
- Bio-based Thermosets: There is a growing trend towards developing environmentally friendly thermoset materials derived from renewable resources.
- Smart Thermosets: Integration of smart materials that can respond to environmental changes, such as temperature or pressure, is on the rise.
- 3D Printing with Thermosets: The use of 3D printing technology is expanding in the thermoset domain, offering new avenues for rapid prototyping and bespoke manufacturing solutions.
The introduction of the newest thermoset molds marks a significant advancement in manufacturing technology. Their unmatched durability, heat resistance, and design versatility make them an invaluable asset in various industries. As innovations continue to evolve, thermoset molds will play a pivotal role in shaping the future of manufacturing, driving efficiency and product quality to new heights. Manufacturers looking to remain competitive must consider leveraging these cutting-edge materials to meet the demands of an ever-changing market landscape.
RELATED NEWS